Environmental protection at Vorwerk Engineering
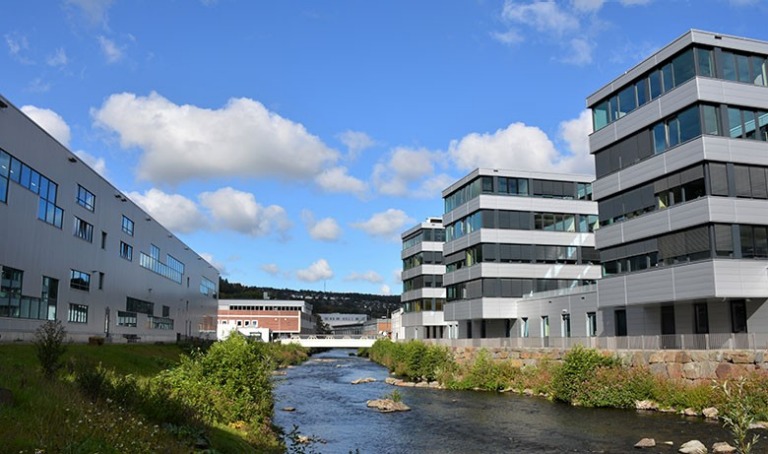
Saving energy, creating natural spaces
Those who protect the environment support people, animals and nature. Not just individuals can do so, an entire plant can, too. In Laaken we at Vorwerk have expanded our production and made it eco-friendlier. The results are reflected in energy-optimized buildings for the engine works, administration and new Innovation Center. We have also improved the river landscape of the nearby Wupper river.
They are constructed in Wuppertal-Laaken: the engines for Thermomix®, Kobold and Co. Between 2016 and 2019 one of the largest modifications in Vorwerk's history took place at our manufacturing base. The demolition of an old production hall in favor of a production facility 20,000 square meters larger in size, which simultaneously takes its surroundings into account, the Wupper river that flows nearby. The “Wupper Süd” project also includes 14,000 square meters for research, development and administration buildings. Today around 1,000 people work in Laaken.
Comprehensive environmental concept for buildings and premises
One of the people who accompanied the restructuring from very close range is Dr. Wilhelm Floer. As the Head of Quality Management Audit, he and his team ensure that all Vorwerk production facilities meet the normative requirements for quality management, environmental management and energy management. In addition, as the coordinator for sustainability at Engineering , he promotes numerous measures to protect the environment.
“For the Wupper Süd project, we dealt with energy and relevant environmental aspects at an early stage. Ranging from the ground conditions through to the building materials used and on to the building technology, there were numerous areas that called for action,” he says.
Heating, ventilation and lighting make a significant contribution to climate protection. Floer and his colleagues have ensured that the waste heat from the machines is used to heat the offices. The Innovation Center has also received a highly efficient heating- and cooling ceiling, the ceiling area thereby ensuring a pleasant climate in the room.
For the engine plant, a four-stage, energy-saving cooling technology was used for which the evaporative cooling of the room air as well as water from the Wupper river are utilized, among other things. “This is how the production covers its own cooling requirements,” Floer explains. All production halls and offices are illuminated using energy-saving LED lamps.
With the construction and conversion of the buildings, the access routes have also changed. The entrances and exits were set up in such a way to reduce the traffic burden on the road. Charging stations for company cars and electric cars of employees and business clients are also available.
Renaturation of the Wupper river: new habitat for humans and animals
It was very important to those involved that the Wupper river, which runs directly past the company premises, should undergo renaturation. In close cooperation with the city of Wuppertal and the Wupperverband water industry association, the riverbed and embankment were altered so that a more natural habitat for animals and plants flourished once more. “Stone islands were set up as river obstacles so the current would slow down,” explains Wilhelm Floer. The Wupper river used to be narrower than it is today. "The natural widening helped not only the animals coming to the river, but also people – as it holds back flooding," he says. A simulation by the Wupperverband has shown that the renaturation of the Wupper river is able to prevent severe flood damage.
Vorwerk invested 400,000 euros in the natural environment. With this amount, 1.1 kilometers of renaturized Wupper river as well as the new Laaken pond could be financed. “The old pond behind Hall B had very poor water quality before construction work began,” says Floer. As chances were slim that it could be saved, a new pond location was found nearby, which now contains clean, fresh water. "The living conditions for fish, amphibians and other small creatures have significantly improved," says Floer. “It is wonderful to witness this when visiting Laaken.” In spring 2021 three toad tunnels were created so that the amphibians in the area could migrate under the road to the pond and back. A tunnel for smooth snakes has been built on the other side of the Wupper. “We are observing the ecological success of the modifications as part of a biology monitoring program,” he explains.
With the changed appearance of the Wupper river and Laaken pond, a local recreational area has sprung into life for employees and residents to enjoy at leisure, which is much appreciated.
The next steps toward climate neutrality
But that's not all. The next step for Wilhelm Floer and his team is imminent. “We are moving toward climate neutrality. From 2022, we as part of the Vorwerk Group will have a neutral effect on the climate," he says. Vorwerk follows the creed "Avoiding – Reducing – Offsetting" in the process.
Floer explains: "We want to avoid or reduce CO2 emissions wherever possible, for example by switching off unnecessary or inefficient energy consumers." Recently, five machines were equipped with more efficient drives, with which Engineering now consumes 700,000 kilowatt hours less per year.
The most important factor for preventing CO2, however, is switching over to green electricity. "We have been purchasing green electricity from Stadtwerke Wuppertal since 2018," says Floer. And soon Engineering will be producing its own electricity from renewable energies: a photovoltaic system is currently in planning on a space of 6,000 square meters on the production hall in Laaken. “With this, we can produce approximately five percent of Engineering 's total consumption ourselves,” explains the sustainability expert.
Where it is not yet possible to reduce CO2 emissions, the Vorwerk Group offsets the remaining emissions. This applies, for example, to the vehicle fleet, whereby vehicles with internal combustion engines are gradually being replaced by electric vehicles.
Less trash, more recycling
Environmental protection also includes avoiding or recycling waste. This already works quite well with the plastics used. "Start-up parts in the injection molding process are ground and reused again," explains Floer. A new mill for plastics was purchased in 2020 for this purpose.
Other waste is collected separately, recycled if possible or otherwise disposed of properly. Between 2016 and 2020 Vorwerk reduced its overall waste by 27 percent. The volume of hazardous waste decreased by almost 60 percent over this period. The recycling rate in 2020 was well over 90 percent.